El domo como ya lo hemos mencionado es el encargado de realizar la conversión final de fase agua / vapor, donde se lleva a cabo una separación final del agua presente en el vapor, por tal motivo el control de nivel en este proceso debe ser muy preciso.
Si el nivel del agua es muy alto, se puede generar arrastre de agua hacia posteriores sistemas como turbinas de vapor, generando de esta manera severas pérdidas. De modo contrario si el nivel es demasiado bajo puede exponer la tubería y por último fracturarse por sobrecalentamiento.
Por otra parte el poder responder ante las constantes demandas de los consumidores de vapor (turbinas, intercambiadores, etc) con gran precisión es otro aspecto de gran relevancia a ser mencionado.
Imagen 1.
Con esta introducción básica ya realizada queremos compartir con ustedes tres tipos de controles usados para el control de nivel los cuales son:
1. Control de nivel de un solo elemento para pequeñas calderas, de magnitudes moderadas y bajas demandas.
2. Control de nivel de dos elementos para medianas calderas de moderadas magnitudes y demandas.
3. Control de nivel de tres elementos para grandes calderas de amplias magnitudes y altas demandas y presiones.
Estrategias de control de nivel de un solo elemento.
En la estrategia de un solo elemento, la medición de nivel en el domo se compara con la referencia y la salida del controlador
ajusta la válvula de alimentación de agua. Este esquema es adecuado cuando las variaciones de la carga son pequeñas y cuando la demanda del flujo de vapor sea menor del 20 % máximo.
Este tipo de control es usado frecuentemente en calderas pequeñas con un gran volumen de agua almacenada y es adecuado siempre que las variaciones de carga no sean muy representativas como lo mencionamos anteriormente, la única variable de proceso presente es el nivel del domo con el cual controlamos el agua de alimentación.
Imagen 2.
En cuanto al sistema de control visto desde un diagrama SAMA (Imagen 2) vemos involucrados el transmisor de nivel del domo (presión diferencial) y el transmisor de presión de vapor en el domo, ambas señales son pasadas a través de un bloque de cálculo el cual en este caso nos compensa variaciones en la densidad del agua y del vapor y así minimizar cambios en las contracciones y expansiones en el nivel.
Imagen 3.
La tendencia superior de la imagen 3 es el nivel del domo y las respectiva contracciones (Shrink) y expansiones (swell) presentes en el domo debido a los cambios en la presión en el domo generados por la demanda de carga la cual hace alterar la densidad o cambios en el suministro de combustible.
Cuando los cambios en la demanda son frecuentes y de gran magnitud se puede utilizar un sistema de control de dos elementos.
El control por dos elementos funciona bien cuando existe una relación aproximada lineal y repetible entre el flujo de vapor; la señal de comando al actuador lineal y el flujo de agua de alimentación.
Cuando se emplea como elemento final de control una bomba de velocidad variable, la relación entre velocidad y flujo de agua es fuertemente no lineal y por lo tanto no es recomendable usar estrategia de dos elementos.
Pero cuando se emplea válvula con una característica de flujo lineal, la estrategia de dos elementos trabaja correctamente. Como la caída de presión sobre la válvula cambia con las condiciones de demanda de vapor, una válvula con característica de igual porcentaje exhibe un comportamiento «aproximadamente» lineal.
Para resumir nuestro control de dos elementos funciona correctamente cuando la relación flujo de agua vs señal de control al actuador lineal es aproximadamente lineal y repetible.
Imagen 4.
En nuestro siguiente diagrama SAMA podemos evidenciar tres distintas variables:
1. Presión de vapor salida del domo.
2. Flujo de vapor salida del domo.
3. temperatura de vapor salida del domo.
Imagen 5.
Estas tres variables son usadas para un cálculo de flujo másico, donde la presión y la temperatura son usadas como compensaciones en la densidad y peso molecular del vapor; a su vez en este cálculo al flujo de vapor se le realiza una extracción de raíz cuadrada para compatibilizar con la medida de nivel la cual es lineal.
El caudal de vapor entra al sumador como señal feedforward para obtener la posición inicial de la válvula.
En la parte izquierda de nuestro diagrama SAMA podemos observa un controlador de nivel el cual es el encargado de reajustar la demanda de agua para mantener dicho nivel en su punto de consigna.
Ahora si cambia el caudal de vapor, la señal feedforward proporciona un cambio inmediato en el caudal de agua con el fin de mantener fijo el nivel. Si después de estabilizarse el caudal de vapor cambia el nivel la señal procedente del controlador reajusta la posición de la válvula para restablecer el nivel deseado.
Teóricamente la ecuación del sumador mencionado anteriormente funciona de la siguiente manera:
S = X + Y – 50
Donde:
S: Salida hacia la válvula de control en %
X: Caudal de vapor expresado en %
Y: Salida del controlador de nivel en %
Restamos 50 % en el cálculo para mantener la salida del controlador en un 50 % (compensación).
Si no tuviéramos en cuenta este valor ocurriría algo como esto:
El flujo másico de vapor debe coincidir con la cantidad de agua aportada por lo que en estado estacionario, en este caso la salida del controlador debería ser 0 %. Si la demanda de vapor aumenta se produce disminución en el nivel aumentando la salida del controlador y así la apertura de la válvula para compensar la pérdida de agua.
De modo contrario si la demanda de vapor disminuye el flujo másico también, produciendo un aumento en el nivel y disminuyendo la salida, en este caso el control no actuaría pues su salida ya se encuentra en 0 %.
En algunos casos este valor de 50 % puede variar dependiendo del porcentaje de purga en la caldera para mantener una conductividad adecuada o para suprimir lodos, si el porcentaje de purga es del 2 % (valor promedio) este debe ser restado al 50 % inicial.
Estrategia de control de nivel de tres elementos.
En ciertas aplicaciones donde se desea minimizar el tamaño del domo, aumentar la velocidad del sistema de agua / vapor, se requiere que la carga en la caldera excede de un 25 a un 30 % de la demanda total de manera rápida y todas las limitaciones existentes en el control por dos elementos quieran ser suprimidas, la necesidad un tercer elemento al controlador es de gran importancia.
Para una mejor comprensión, hemos desglosado de la siguiente forma.
Imagen 6.
En el sistema de la imagen 6, se mantiene la entrada del agua igual que la demanda de vapor, utilizando tres variables de proceso, nivel del domo, caudal de vapor y caudal de agua de alimentación.
Desde el punto de vista del cálculo, el comportamiento del vapor y el nivel (control por dos elementos es el mismo), la principal diferencia ahora radica en que a la salida del sumador ( Σ ) es enviado como setpoint al controlador de agua de alimentación en lugar de enviarlo directamente al elemento final de control.
Por medio del controlador de agua se compensan las alteraciones que se producen por falta de repetibilidad o no linealidad del elemento final de control cuando variables como la presión del agua no es estable.
Imagen 7.
En cuanto a la imagen anterior (7) la señal de flujo de vapor la cual representa la demanda de carga, se utiliza como señal de adelanto o feedforward para fijar el setpoint del controlador de agua de alimentación.
La operación teórica que ejerce el sumador en este caso es la siguiente:
S = K1 * X +Y – K2
S= Salida del sumador
X= Medida de flujo de vapor
Y= Salida del controlador de nivel (50%)
K1= Rango de medidor vapor (flujo másico) / rango de medidor agua (flujo másico)
K2= 50 % – (Porcentaje de purga de la caldera).
Notas: En nuestro caso se pretende que la salida del controlador sea (50%) cuando no exista un desequilibrio entre la medida y setpoint para permitir que el controlador de nivel tenga un margen de trabajo tanto si aumenta como si disminuye la producción de vapor.
Por otro si no existiera K2 y si la entrada de agua estuviera equilibrada con la producción de vapor, tanto la salida del controlador de nivel como la salida del sumador serian igual a cero y así ante una disminución en la producción de vapor el controlador no tendría margen de trabajo para disminuir la entrada de agua.
Imagen 8.
S = K1 * X +Y – K2
S= Salida del sumador
X= Medida de flujo de vapor
Y= Salida del controlador de nivel (50%)
K1= Rango de medidor vapor (fkujo másico) / rango de medidor agua (flujo másico)
K2= 50 % – (Porcentaje de purga de la caldera).
Ejemplo practico:
Rango de medidor de vapor: 0 – 40 Tm / h
Rango de medidor de agua: 0 – 35 Tm/ h
Producción de vapor: 30 Tm/ h
X = 100 * 30 / 40 = 75 %
K1= 40 / 35 = 1.142
La salida del sumador sera:
S = 1.142* 75 + 50 – 50 = 85,65 %
De esta manera la salida hacia el controlador de agua alimentación como setpoint sera:
Caudal de agua = 85,65 * 35 / 100 = 29.9 Tm / h
Lo cual significa que para generar 30 Tm / h de vapor, se requieren 29.9 Tm / h de agua.
En estado estacionario la salida del controlador sera 50 % para tener un margen de trabajo por si aumenta o disminuye la producción de vapor.
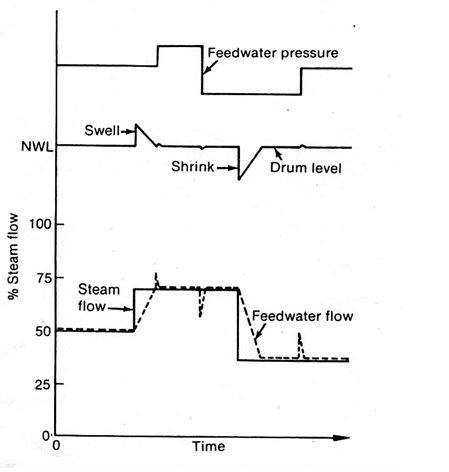
- Control avanzado de procesos – J acedo Sanchez -Pag 390.
- Cuaderno profesional AADECA N°4 Vol II 1994.